PART 2: Checking The Fuel Injector Spray Pattern
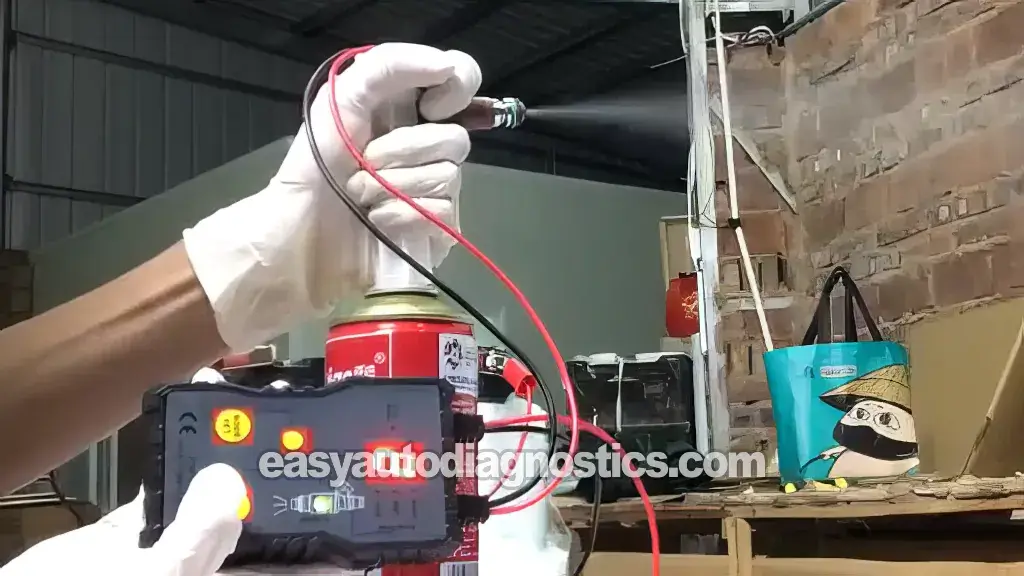
So far, you've confirmed that the fuel injector's internal resistance is within the indicated specification, meaning it doesn't have an internal open or short-circuit issue.
Next, you'll need to remove the fuel injector and with a DIY fuel injector cleaning tool (which you can buy online) along with a can of brake cleaner, you'll activate it to check if it sprays properly.
This fuel injector cleaning tool kit includes two important components:
- A 12 Volt power module that triggers the fuel injector in pulses, similar to how the fuel injection computer does it.
- An adapter that connects the fuel injector to a spray can of brake cleaner.
Once you've set up the test, a properly functioning fuel injector will spray the brake cleaner in a fine mist. If the injector is clogged or malfunctioning, it'll either squirt the brake cleaner or not spray at all.
The cool thing about this fuel injector cleaner took kit is that it's not expensive. You can purchase it here:
- QX Fuel Injector Tester & Adapter for Diagnosis and Cleaning of Injectors DIY Cleaning Tool Kit (at: amazon.com).
- EM276SET Fuel Injector Tester & Adapter DIY Cleaning Tool Kit Set (at: amazon.com).
IMPORTANT: Before installing the same or new fuel injector back on the fuel injector rail, take a look at: Important Tips For Installing A Fuel Injector.
CAUTION: Use safety glasses when performing the fuel injector cleaning procedure.
Alright, these are the test steps:
- 1
Remove the fuel injector.
- 2
Connect the fuel injector to the plastic adapter.
NOTE: I've found that securing the fuel injector to the adapter with a thick rubber band helps to make the whole process easier and less messier. - 3
Connect the fuel injector to the tool's power module.
NOTE: Follow the tool's safety and recommended set-up instructions. - 4
Connect the cleaning kit's power module to your pickup's battery.
- 5
Connect the fuel injector/adapter to a spray can of brake cleaner and press them onto the spray can.
- 6
Activate the power module.
- 7
The fuel injector should spray fuel in a fine mist and in a conical shape.
Let's interpret your test result:
CASE 1: The fuel injector did not spray at all. This tells you that the fuel injector is bad and needs to be replaced.
CASE 2: The fuel injector sprayed the brake cleaner in a fine mist and in a conical pattern. This tells you that the fuel injector is OK.
CASE 3: The fuel injector sprayed the brake cleaner in a squirt or a stream (not in a fine mist). This tells you that the fuel injector is dirty/clogged.
Continue cleaning the fuel injector until it starts to spray in a fine mist. If the cleaning it doesn't restore the injector's spray pattern to that of a fine mist, you'll need to replace it.
Important Tips For Installing A Fuel Injector
When installing a fuel injector (whether it's the same one or a new one) on the fuel injector rail, keep in mind the following important suggestions to ensure everything runs smoothly and safely.
- Always use new fuel injector O-rings: When installing a new or the same fuel injector on the fuel injector rail, it's super important to use new O-rings. New fuel injectors usually come with new O-rings, but if you're reusing an old injector, you'll need to buy them. The new O-rings will ensure a secure seal and prevents gasoline and vacuum leaks.
- Lubricate the new fuel injector O-rings: Before placing the new O-rings onto the injector, coat them in a thin layer of clean engine oil (5W-30 or lighter). Avoid using silicone-based greases or other lubricants.
Lubricating the O-rings with light engine oil helps in inserting the fuel injector into both the injector rail and the intake manifold port. Making sure the O-rings aren't damaged during installation is critical because any damage could lead to gasoline or vacuum leaks, which you definitely want to avoid. - Replace damaged connector: If the fuel injector's connector is damaged in any way, replace it with a new one. It's not uncommon for the locking tab of the fuel injector to break; if it's broken, replace the connector.
Also, avoid using butt connectors to join the new connector's wires to the engine wiring harness. Butt connectors are notorious for eventually losing their grip on the wires, causing false contact issues. Instead, solder the wires for a permanent repair.
Remember, the whole idea here is to prevent gasoline leakage and avoid the risk of a fire. So take your time and ensure everything is properly seated and secure.
Precautions To Take When Removing The Intake Manifold Plenum
Before you remove the intake manifold's plenum, keep in mind several important things:
- Buy or borrow a repair manual (preferably a Haynes Repair Manual -Chilton manuals suck) so that you can have the intake manifold removal process explained in detail.
- The manual will also give you the torque specifications for the bolts.
- Disconnect the battery from its negative (-) cable before removing the intake manifold plenum and leave it disconnected during the entire fuel injector testing procedure.
- Be careful that no foreign object, like a bolt, a nut, or any metal piece/part, falls into the open manifold port runners.
- Once the plenum has been removed, place a clean rag or rags on the open intake runners. This will keep things from falling into them.
- As you're removing bolts, nuts and stuff from the intake plenum to remove it, place them in a container and away from the engine compartment.
- Never crank the engine with the plenum removed from the lower intake manifold.
Anything falls into the open intake runners, without you knowing, and the engine is started, you are going to be in a big world of hurt! Since it may require the removal of the cylinder head to retrieve the part that fell in. So be alert and be careful.
Removing the plenum is not an out of this world thing that no one can do, it's done around the country in many shops without complications or unhappy endings by simply following some precautions.
More 4.2L Ford Diagnostic Tutorials
You can find a complete list of 4.2L Ford F150/F250 tutorials and wiring diagrams in this index:
Here's a small sample of the tutorials you'll find in the index:
- How To Do An Engine Compression Test (1997-2008 4.2L V6 Ford F150, F250).
- How To Test The Throttle Position Sensor (1997-2000 4.2L V6 Ford F150, F250).
- How To Test The Ford EGR Valve EGR Vacuum Solenoid, DPFE Sensor.
- How To Test The Coil Pack (Ford 3.0L, 3.8L, 4.0L, 4.2L).
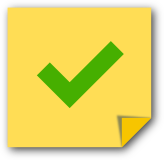
If this info saved the day, buy me a beer!
