Interpreting The Compression Test Results
The engine cylinders usually wear out at the same rate, unless they have suffered some sort of mechanical problem.
If the compression values vary too much, the engine will suffer a rough idle or a misfire problem that will light up the check engine light with a misfire trouble code.
The key to finding out is to do some math and see if the lowest compression value you got differs by more than 15% of the highest value.
You can do this by using my online low compression calculator here: Online Low Engine Compression Calculator or, as I mentioned before, by calculating this 15% difference manually.
To explain how to figure out this 15% thing manually, let's say that I got the following compression test results from a 4.0L Jeep Cherokee (Wrangler):
- Cylinder #1 175 PSI.
- Cylinder #2 165 PSI.
- Cylinder #3 170 PSI.
- Cylinder #4 120 PSI.
- Cylinder #5 160 PSI.
- Cylinder #6 170 PSI.
My next step is to do the following calculation:
- I'll multiply 0.15 (15%) by the highest value: 175 x 0.15. This gives me 26.25, but I'll round it out to 26.
- Next, I subtract 26 from 175: 175 - 26 = 144.
- So now I know that the lowest possible compression value the engine can have is: 144 PSI.
This means that cylinder #4, which has a compression value of 120 PSI, is the one causing the misfire because it's below the 144 PSI minimum.
To find out if the compression values you got from your engine compression test are good or bad, you'll need to do the same calculation. Of course, you'll need to use the highest compression value you got and not the one in the example.
Once you've found the 'dead' cylinder, the next step is to find out what's causing the low compression value. For this step, go to: TEST 2: Wet Compression Test.
TEST 2: Wet Engine Compression Test
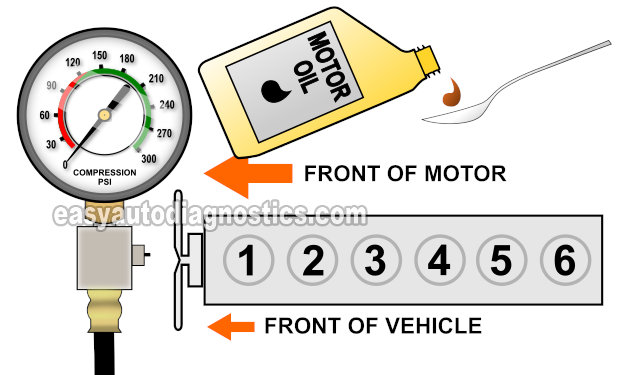
If in TEST 1 you got one or more compression values that are lower than the rest, then your next is to do a 'wet' compression test.
All that's involved is adding about 2 tablespoons of engine oil to the cylinder with low or 0 PSI compression. Then the cylinder's compression is tested again.
If the compression value increases, from the value you got in TEST 1, then you can conclude that the low compression problem of that cylinder is due to bad piston rings.
If the compression value does not increase, then you can conclude that that cylinder's compression problem is due to bad or damaged cylinder head valves.
These are the test steps:
- 1
Add 1 or 2 tablespoon of engine oil in the cylinder you need to retest. I suggest using a small and long funnel so that the oil will reach the inside of the cylinder.
- 2
Install the compression gauge on the cylinder you just added oil to.
- 3
Have your helper crank the engine till the needle stops climbing on the compression gauge.
- 4
You'll see one of two results:
1.) The needle will climb higher than the previous compression number you recorded for this specific cylinder.
2.) The needle will not move at all or stay at the same number you recorded earlier.
What ever value your compression tester reads, write it down again. - 5
Repeat steps 1 thru' 4 on any other cylinder you need to check.
Let's examine your test results:
CASE 1: The compression value increased. This test result tells you that the low or near 0 PSI compression value is due to worn out piston rings of that specific cylinder.
CASE 2: The compression value DID NOT increase. This test result confirms that the cylinder head valves of that cylinder are worn-out or damaged.
More 4.0L Jeep Cherokee Tutorials
You can find a complete list of diagnostic tutorials and wiring diagrams for the 4.0L Jeep Cherokee here:
Here's a sample of the tutorials you'll find in the index:
- Ignition System Wiring Diagram (1993-1995 4.0L Jeep Cherokee)
- How To Test For A Blown Head Gasket (1993-2001 4.0L Jeep Cherokee)
- How To Test The Crankshaft Position Sensor Jeep 4.0L (1993-1995 4.0L Jeep Cherokee)
- How To Test The Front O2 Sensor Heater (1996 4.0L Jeep Cherokee)
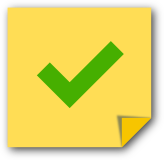
If this info saved the day, buy me a beer!
